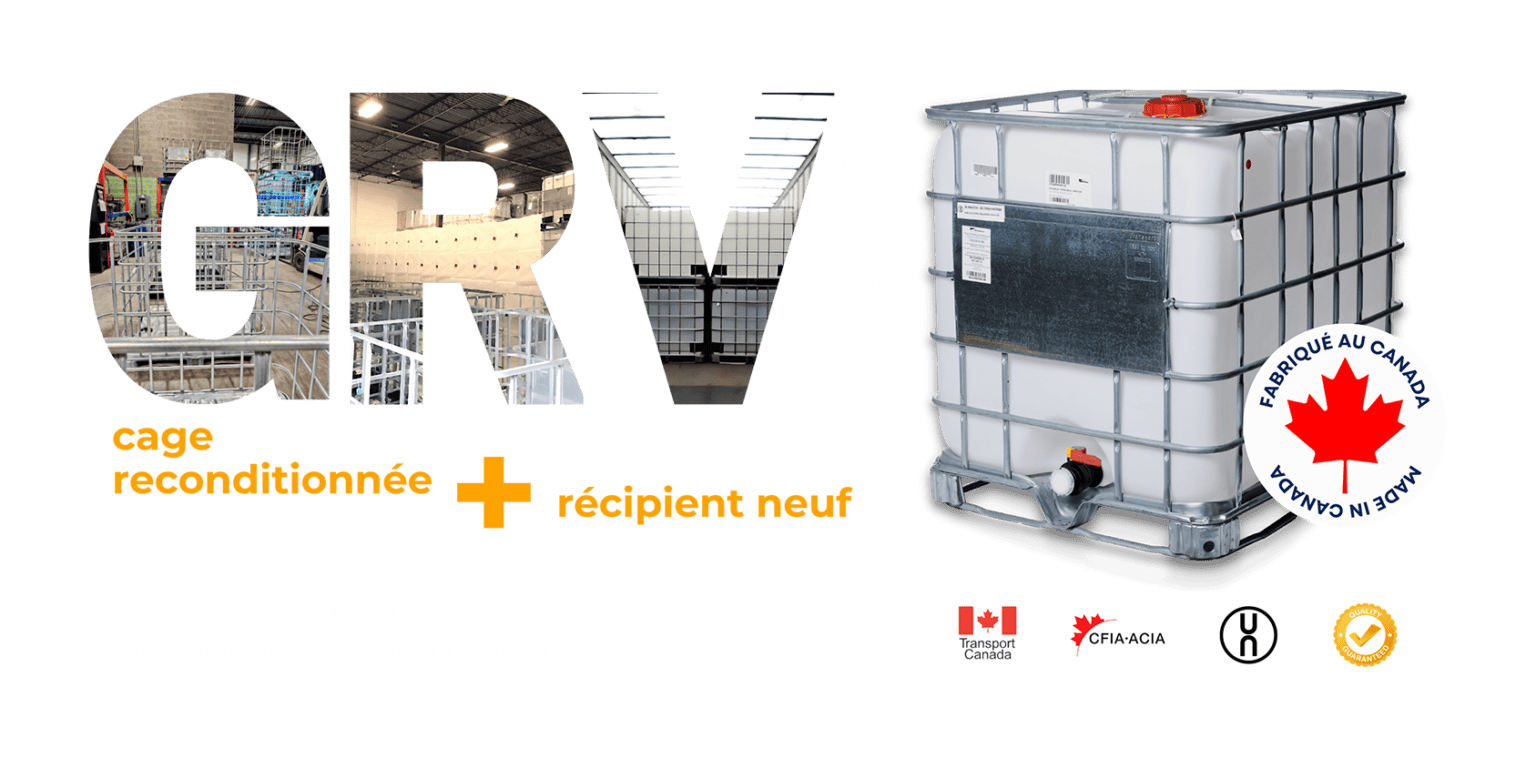
Production of IBC TOTE hybrid
With its unique know-how, Distribution Robitaille stands out from the crowd. We specialize in the production of hybrid IBCs( reconditionedIBC totes ). This approach combines significant savings with a strong environmental commitment.
Our 1000L and 1300L totes are precision-engineered to meet the sector’s most demanding requirements. They meet the industry’s most stringent requirements. What’s more, they are Transport Canada certified.
As one of the few manufacturers of this innovative product in Quebec, our company is a true entrepreneurial success story.
In concrete terms, our hybrid IBC production process involves a crucial step. We meticulously recondition the protective cage. Then we integrate a completely new tank. This ingenious approach enables us to use a wide variety of products. This is done without any risk of cross-contamination. As a result, this method significantly reduces operational costs for our customers. We offer a safe and cost-effective solution.
A reliable solution, proudly designed in Canada
Our authentically Canadian product is bottled and distributed from Saint-Hyacinthe, in the heart of Quebec. This central location ensures efficient logistics and optimal local service.
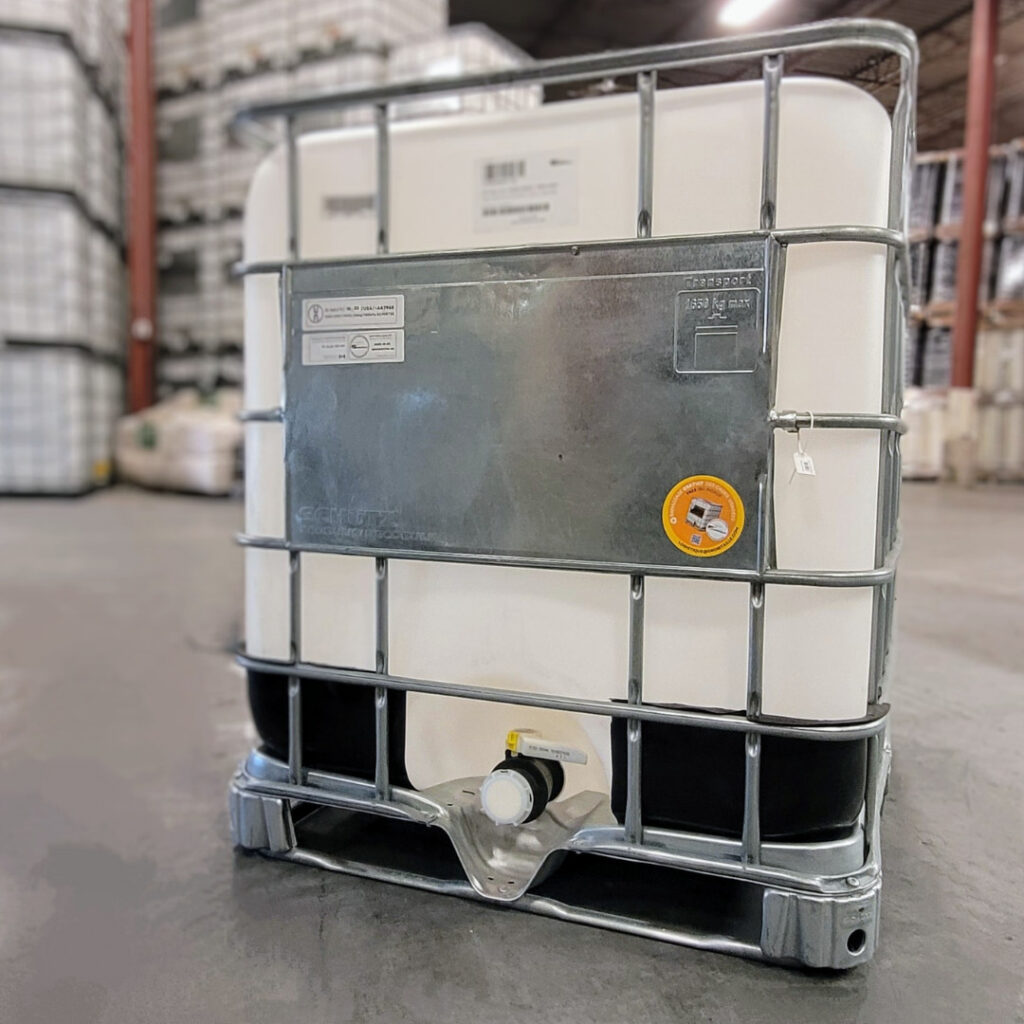
A high-quality product, made in Canada.
51019
IBCs produced since 2017
"We are one of the few companies certified by Transport Canada".
Distribution Robitaille is a Transport Canada-certified IBC re-bottler, ensuring that every step of the process is carefully planned and rigorously executed.
When purchasing an Bulk/IBC tote 1000L or 1300L for the transport of dangerous goods, check that the supplier has a certificate of registration from Transport Canada.
U.N. standardized IBCs are designed, manufactured and tested according to specific criteria to guarantee their resistance to transport conditions.
Manufacturers in Canada must follow the ISO 9001 standard.
Quality control is our top priority.
Each rebuilt U.N. composite tote IBC undergoes two inspections. The first inspection takes place during cage preparation, when each metal cage is checked before any container is installed.
A second inspection is carried out once the container has been installed and secured with metal bars.
After a satisfactory final inspection, a label is affixed to the outer envelope of the tote IBC on the valve side, bearing the registration certificate number, the quality control certificate, and contact details for returning the cages.
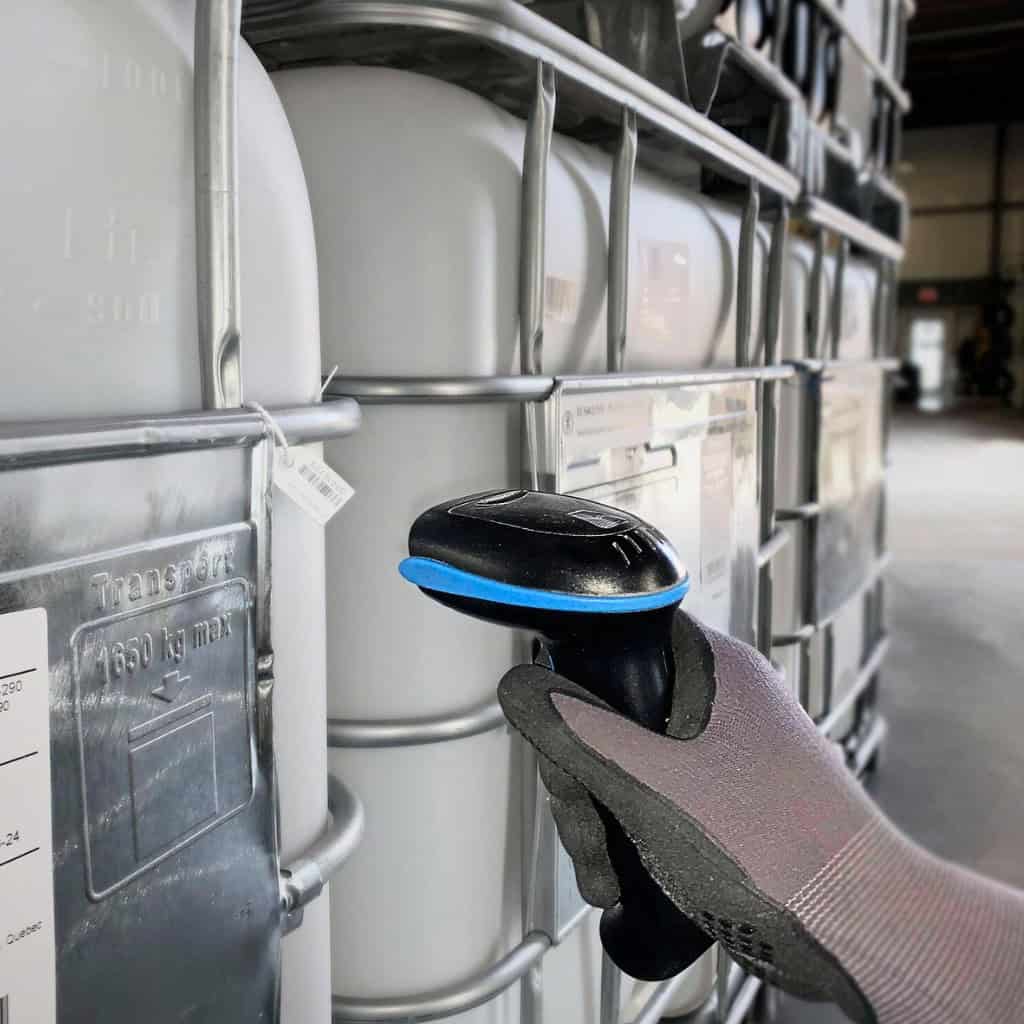
We ensure exceptional service through strict quality control.
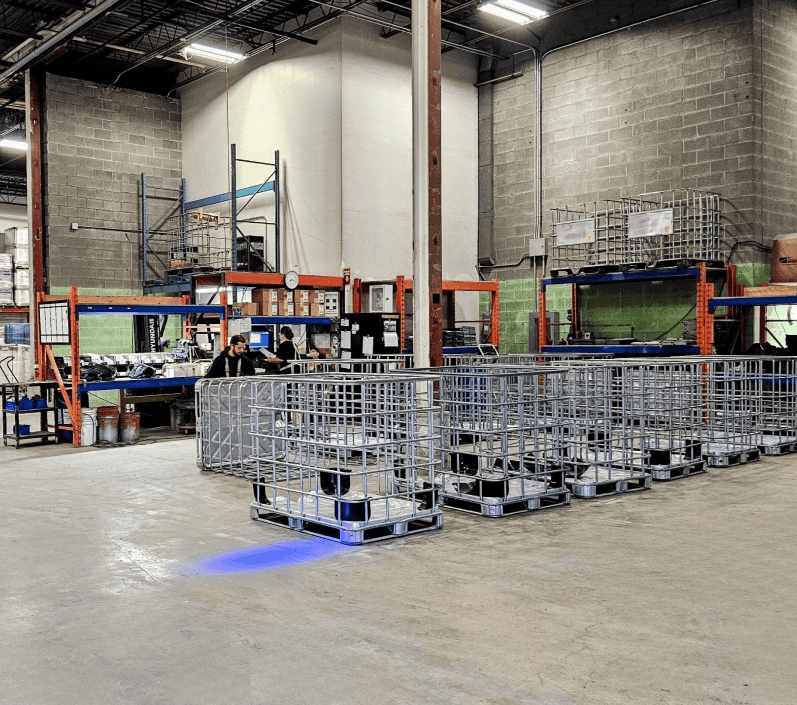
Inspection and preparation of metal cages
An initial inspection is carried out when the metal cages are prepared, to check their condition before the containers are installed. Repairs or replacements on standardized IBCs must comply with the same specifications as the original parts.
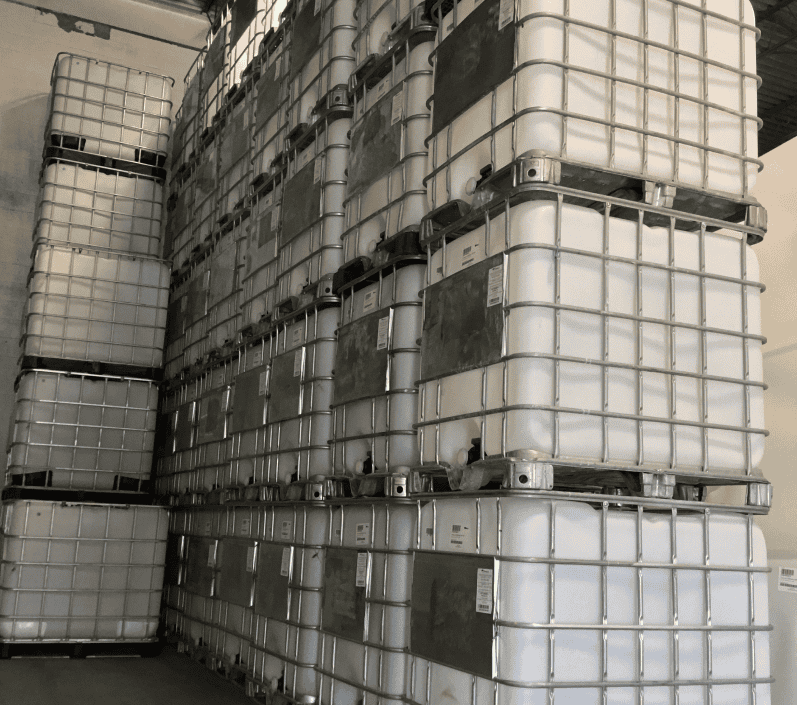
Installing the new reservoir
When replacing the plastic inner container of a standardized composite IBC, the new container must be of the same specification as the original. The installed container is brand new, sealed at the cap and valve by the manufacturer, guaranteeing the absence of any contaminants.
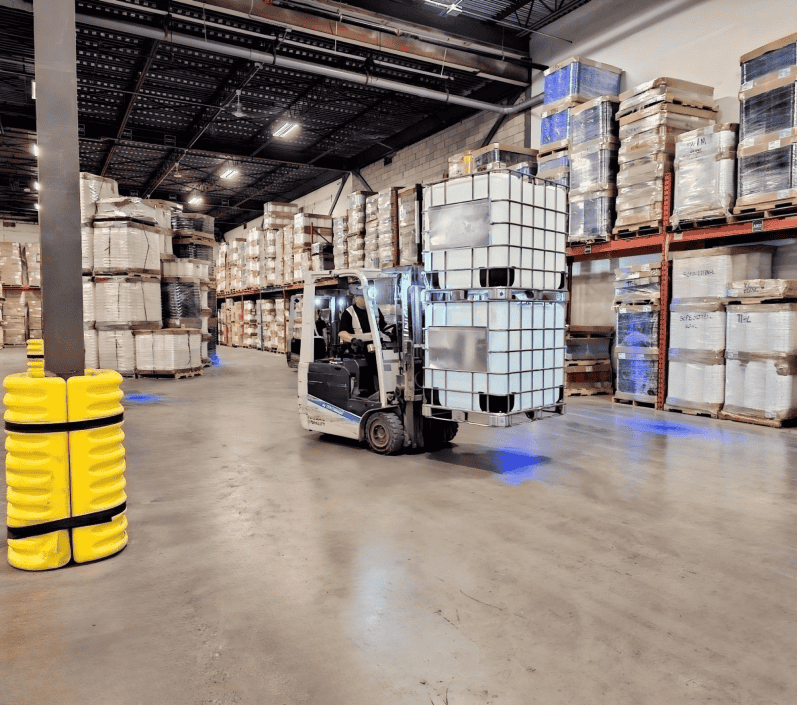
Final inspection?
An external inspection is carried out at the end of the assembly line and during order picking to identify any anomalies on the final products.